Additive manufacturing (or 3D printing / 3D prototyping as its also known) allows manufacturers to create physical, three-dimensional objects directly from a computer design file. The technology used is similar to a desktop printer but instead of ink, 3D printers use a wide variety of materials, the most common being metals, polymer composites and ceramics.
Real time industrial temperature control and measurement is an essential part of additive manufacturing. In this post, we take a quick look at why this is and some of the different situations in which we can help with this.
Additive Manufacturing Processes and 3D Prototyping
Additive manufacturing started as a way of 3D prototyping or in other words, producing prototypes in a more efficient way. However, it has now become more and more common in use by manufacturers to make parts which could not easily have been produced via other traditional manufacturing processes. Metal part production is the fastest growing area of additive manufacturing and the biggest sector of the industry.
Additive manufacturing can significantly reduce energy and waste and improve productivity when compared to more traditional methods of production. There are a number of different methods, one of the more common of which is by using a laser.
Additive Manufacturing Processes and Parameters
Additive manufacturing is a thermal process meaning the material used is heated to or near its melting point as the item is created. The material is then applied gradually in layers to create the object.
During the production process, there are a number of factors that can affect the quality of the 3D object produced, temperature being one of the most important. For example, higher temperatures may produce a heavier and higher quality product, with products made at higher temperatures showing higher yield stress and lower strain at break. Items produced at lower temperatures may have greater air gaps in them, resulting in decreased strength.
Heat and temperature control are therefore crucial, and it is often essential to be able to monitor, measure and control different parts of the different equipment. For example, you may need to measure the temperature of the laser itself as well as the surface of the object being produced. It is also often important to have highly accurate and consistent measurement of preheating processes, and heating up and cooling down processes.

Lasers in metal applications
There are two common laser methods used in 3D metal production and they operate at 1064 nm and 10600 nm respectively. The laser beam creates a melt pool on the surface of the object and then metal powder is distributed onto the surface, layer by layer to create the product.
The melt pool temperature is very important as it’s got to be hot enough to melt the material but not so hot as to destroy it.
Temperature Measurement and Thermal Processing
At Process Parameters we have a range of equipment that enables us to deliver highly accurate temperature measurement in a range of different situations including for metal, glass and plastic and including both pyrometers and cameras. Using this infrared technology, we can measure temperature in a non-obtrusive way, to give real time results, and ensure consistency and control over the additive manufacturing processes.
Metal, in particular, can have an exceptionally high melting point presenting a challenge for tracking real-time temperatures during the additive manufacturing process. However, we have specialist accessories that ensures our equipment can continue to operate safely and accurately even at very high temperatures.
On and off-axis measurement
Using the Optris range of infrared sensors, we can monitor the temperature in one of two ways, namely on axis and off axis.
On axis, requires the installation of the sensor within the laser optic and will measure the temperature of both the laser itself and the surface temperature. This provides real time information about the heating process and whether anything has gone wrong (i.e. pollution on the surface or if the material is cooling too fast, all of which can affect the quality of the product).
We can also measure any pollution on the optic itself such as dirt or dust. Pollution can affect the transmission of heat so instant feedback about this is vital because again, it will affect the quality of the product produced.
As the name suggests, off axis temperature measurement is done externally and measures a broader area of heat distribution rather than just the area of impact from the laser. It also allows for measurement of the distance between the nozzle and the surface so that this can be monitored and controlled.
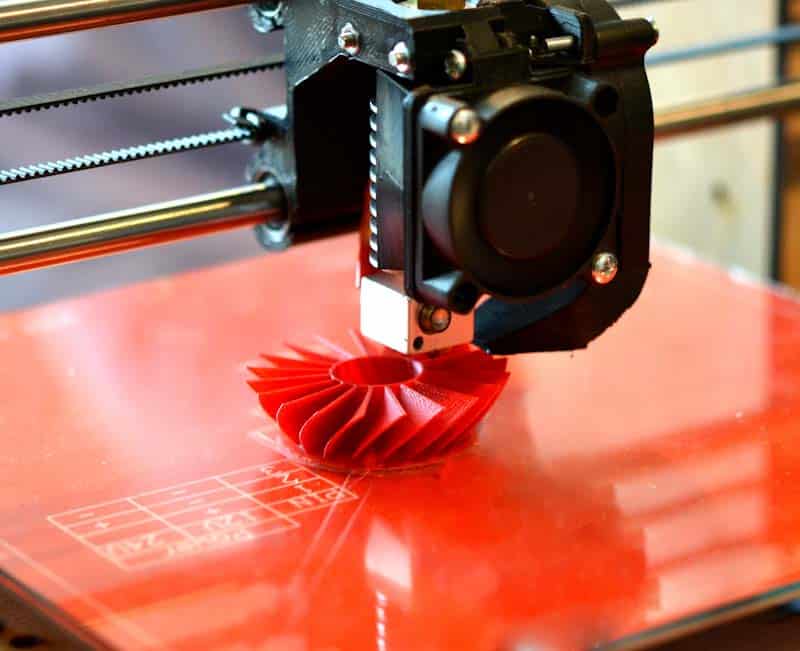
Industrial Temperature Control Company
The equipment you require will of course vary from project to project. At Process Parameters, an industrial temperature control company, we can supply a number of industrial temperature sensors and infrared cameras. One example is the Optris PI 08M Thermal Infrared Camera. This is sensitive to a spectral range of 800 nm and a continuous measurement range from 575 °C to 1900 °C.
We can also supply the Optris PI 05M Thermal Imaging Camera which is a shortwave length camera that also blocks all radiation above 540nm, so can be used successfully with all laser processing applications. It’s ideal for molten metals and metallic surfaces ranging from 900°C-2000°C without sub-ranges. Read more on thermal imaging for energy efficiency.
For glass applications, we can supply the Optris PI450 G7 VGA Thermal Imaging Camera which has been specially designed to take accurate thermal images of glass and is suitable for a variety of applications in the glass industry, anything from glass beads to large panes. These are just some of the different specialist cameras that we can supply for different processes and situations.
If you’d like more information about our products, a particular application or how we can assist, see our contact details or email us now.
Real time infrared images at high speed
Temperature range 575°C to 1900°C
License free PIX Connect analysis software
Up to 764×480 pixel resolution for spotting small hot spots
Special narrow-band spectral response at 800 nm ideal for almost all NIR and CO2 laser processing applications
Adaptor for conversion of USB to Ethernet for Optris infrared cameras
Bridging of up to 100 metres via Ethernet and up to 500 metres via fibre optic cables
Maintains maximum frame of camera for fast processes
Automated process control
Multiple configurable inputs and outputs
Alarm or analogue outputs for easy integration
Self monitoring for safety applications