What is a thermocouple? How do Thermocouples work?
What is a thermocouple? A thermocouple is a device for measuring temperature. It comprises two dissimilar metallic wires joined together to form a junction. When the junction is heated or cooled, a small voltage is generated in the electrical circuit of the thermocouple which can be measured, and this corresponds to temperature.
In theory, any two metals can be used to make a thermocouple but in practice, there are a fixed number of types that are commonly used. They have been developed to give improved linearity and accuracy and comprise specially developed alloys.
Thermocouples can be made to suit almost any application. They can be made to be robust, fast responding and to measure a very wide temperature range.
View our range of thermocouples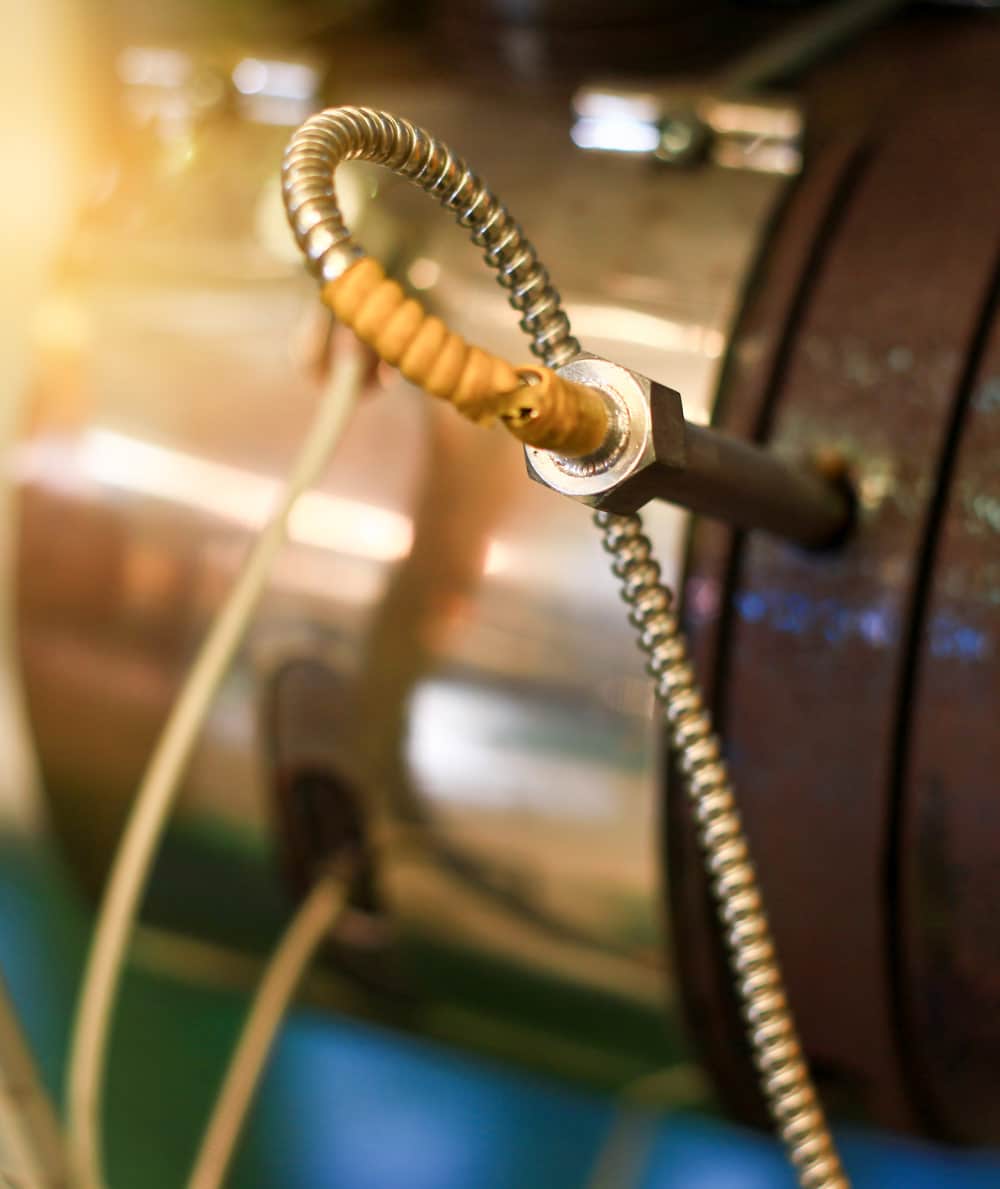
A title
Image Box text
Our Thermocouple range
What does a thermocouple do?
A thermocouple is simply a sensor that is used for measuring temperature. This design of sensor consists of two dissimilar metal wires which are joined together at one end, connected to an instrument that is capable of accepting a thermocouple input and measure the reading. Thermocouples can provide temperature measurements over a wide spectrum of temperatures dependent on which thermocouple type you use.
Discover our range of thermocouple sensors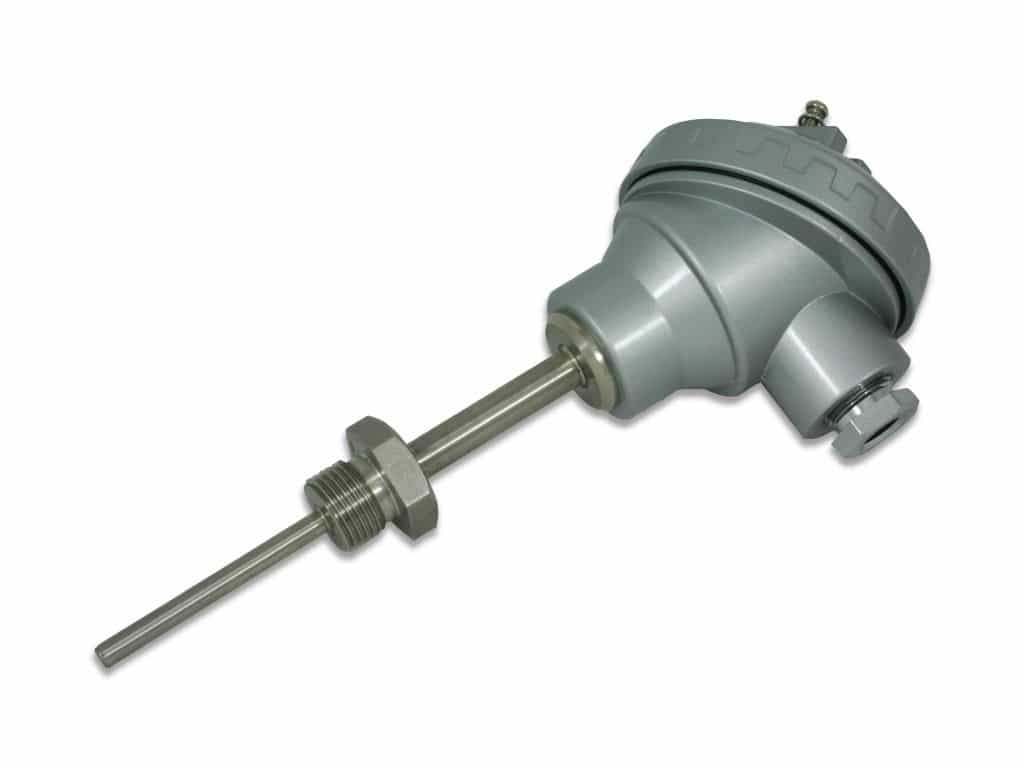
Example of a Thermocouple manufactured by Process Parameters
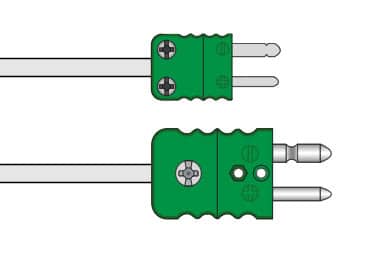
Thermocouple diagram
Thermocouple Working Principle
A thermocouple is a temperature measurement device that operates based on the principle of the Seebeck effect. Thomas Seebeck discovered the continuous current flow in the thermoelectric circuit in 1821. It consists of two different types of metal wires or conductors that are joined at one end to form a junction. When this junction, also known as a measuring instrument, is exposed to a temperature gradient (a difference in temperature between the two ends), it generates a voltage that is approximately proportional to the difference between the temperatures of the two junctions. This voltage is called the thermoelectric voltage and is used to measure temperature in various industries.
Types of Thermocouple Temperature Sensors
What is a Thermocouple Probe?
What is the definition of a thermocouple? Now we have an understanding of how a thermocouple works and what thermocouples are, one of the popular questions is what is a thermocouple probe?
A thermocouple probe is the design of the sensor that it is made in. Whether the sensor is a thermocouple type K, J, T, N all of these thermocouple types can be manufactured in the same size tube, housing or construction.
To get an idea of the typical design available, it is important to consider factors such as chemical resistance, abrasion resistance, and most importantly, vibration resistance. These factors will determine the best thermocouple probe for your specific application. Check out some of our thermocouple sensors to find the perfect fit for your needs.
What does a thermocouple look like? Thermocouples look different due to the constructions they are manufactured in. Although a thermocouple itself is two bare wires joined together, these two wires can be put inside various constructions to protect them so they last longer.
What is a type K thermocouple?
A popular question asked is what is a type K thermocouple?
A type K Thermocouple is made up of two dissimilar metals which are Nickel-Chromium / Nickel-Alumel. Type K is the most popular type of thermocouple because it is inexpensive, accurate, reliable (depending on the design used for your application) and covers a wide temperature range.
Type K thermocouples can be found in a broad range of applications due to its expansive temperature range capabilities. The maximum continuous temperature is up to around 1100 Deg C.
Thermocouples with a plug or cable can be identified by their colour coding. In this case type K is green. If you have a cable the green leg is positive and the white leg is negative.
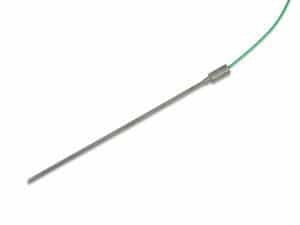
Type K Thermocouple
What is a type J thermocouple?
So what is a type J thermocouple? Type J Thermocouples are also very common. It has a smaller temperature range than a type K thermocouples with a range of 0 to 600 Deg C. The Type J is made up of two dissimilar metals which are Iron / Copper-Nickel (Also known as Constantan). Cost-wise, type J thermocouples are very similar to type K, and some come with an additional sheath for insulation to prolong their life.
One of the most popular applications you find type J being used is in the plastics industry.
Thermocouples with a plug or cable can be identified by their colour coding. In this case type J is Black. If you have a cable, the black leg is positive and the white leg is negative.
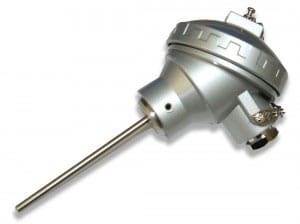
Type J Thermocouple
Frequently Asked Questions
What is the purpose of a thermocouple?
The purpose of a thermocouple is to measure temperature accurately in various applications. It consists of two different metal wires joined at one end, which generate a small voltage when exposed to temperature differences. This voltage can be measured and converted into a temperature reading, making thermocouples essential in industrial processes, HVAC systems, and scientific research.
What is the thermocouple junction and why is it important?
The thermocouple junction is the heart of the whole operation! It’s the spot where two different metals are joined together.
Here’s why it matters:
- The thermoelectric effect: When you have two dissimilar metals connected and there’s a temperature difference between them, a tiny voltage is created at the junction. The hotter this junction gets, the bigger the voltage.
- Temperature measurement: By measuring this voltage with a special instrument, we can figure out the temperature at the junction. So, the thermocouple junction acts like a tiny thermometer that uses electricity!
Basically, the thermocouple junction is like a temperature sensor all on its own. If it’s not working properly, your whole temperature reading will be off. That’s why it’s important to ensure a good connection and protect the junction from damage.
What materials are thermocouples made from (copper alloys, etc.)? Understanding thermocouple probes and sheaths.
Thermocouples are like tiny tag teams – they rely on two different metals to work their magic. The specific metals used determine the temperature range a thermocouple can handle. Here are some common options:
- Type K thermocouple: Often uses chromel and alumel (nickel-chromium alloys) for a wide temperature range.
- Type E thermocouple: This high-temperature thermocouple might use alloys like constantan and chromel.
- Noble metal thermocouples (Type R, S, or B): These use precious metals like platinum and rhodium for extremely high temperatures.
Sheath materials also play a role:
- Stainless steel: A popular and versatile choice for many applications.
- Incoloy: Used for high-temperature environments due to its strength and oxidation resistance.
- Teflon: Can be used for low-temperature applications or when chemical resistance is needed.
There are many other options, so get in touch with our experts who can help you choose the right materials for your specific needs.
Both thermometers and thermocouples are in the temperature measurement business, but they go about it in different ways.
Here’s a breakdown to understand the key differences:
How they work: A classic thermometer uses a liquid (like mercury) or a metal strip that expands or contracts with temperature changes. The movement is then displayed on a scale, giving you a reading. Thermocouples, on the other hand, are based on something called the thermoelectric effect. They use two different metals joined together. When there’s a temperature difference between the junction and another part of the thermocouple, a tiny voltage is created. By measuring this voltage, we can determine the temperature.
Accuracy: Generally, thermometers are good for everyday use where super high precision isn’t critical. Thermocouples can be very accurate, but they might require regular calibration to ensure they’re measuring correctly.
Temperature range: Thermometers typically have a limited range, suitable for everyday applications. Thermocouples are superstars when it comes to handling extreme temperatures, from way below freezing to scorching hot! Different types of thermocouples are suited for various ranges.
Applications: We use thermometers for all sorts of things, from checking your body temperature to monitoring the weather. Thermocouples are often used in industrial settings, like measuring temperatures in furnaces or kilns. They’re also used in science labs and even in some high-end appliances.
So, to sum it up:
- Thermometer: Simple, easy to use, good for everyday temperature measurement.
- Thermocouple: More complex, wider temperature range, often used in industrial applications or for high-precision needs.
What is the working principle of a thermocouple?
The working principle of a thermocouple is based on the Seebeck effect. When two dissimilar metals are joined at one end and exposed to a temperature difference, they generate a small voltage. This voltage is proportional to the temperature difference between the junction and the reference point. By measuring this voltage and using calibration data, accurate temperature readings can be obtained.
What is a thermocouple good for?
Thermocouples are incredibly versatile because they can handle a wide range of temperatures, from super cold to scorching hot.
This makes them perfect for various applications:
- Industrial settings: Measuring temperatures in furnaces, kilns, engines, and basically any industrial process that involves extreme heat.
- Cooking: They’re used in some high-end grills and smokers to precisely monitor cooking temperatures.
- Science labs: Scientists use them in experiments to track temperature changes.
- Everyday life: You might even find them in your home thermostat, helping to regulate your indoor temperature!
Their durability, wide temperature range, and relatively low cost make them a popular choice for many temperature measurement needs.
What causes a thermocouple to fail?
- Physical damage or breakage
- Corrosion or chemical contamination
- Electrical interference
- Thermal cycling fatigue
- Calibration drift over time
- Improper installation or wiring
- Extreme temperatures exceeding the thermocouple’s range
- Mechanical stress or vibration
- Manufacturing defects
- Oxidation of the metal wires
What are the advantages and disadvantages of thermocouples?
Thermocouples are fantastic for many reasons, but like most things, they have some drawbacks too:
Advantages:
- Wide temperature range: They can handle a vast temperature spectrum, from very low to extremely high.
- Relatively low cost: Compared to other temperature sensors, thermocouples are generally affordable.
- Fast response time: Some types of thermocouples can react to temperature changes quickly.
- Durable: They can withstand harsh environments and vibrations.
Disadvantages:
- Accuracy: While they’re good for most applications, they might not be the most precise option for situations requiring super high accuracy. For those cases, other sensors like RTDs (Resistance Temperature Detectors) might be better suited.
- Calibration: Thermocouples need regular calibration to ensure they’re measuring temperatures accurately.
- Cold junction temperature: The temperature at the unconnected ends of the wires (cold junction) needs to be stable for accurate readings.
Thermocouple vs. RTD: Which temperature sensor is right for me?
Both thermocouples and RTDs (Resistance Temperature Detectors) are popular for measuring temperature, but they each have their strengths. Choosing the right one depends on your specific needs.
Here’s a breakdown to help you decide:
Thermocouples:
- Pros: Wider temperature range (from super cold to very hot!), durable, fast response time, generally more affordable.
- Cons: Less accurate than RTDs, need regular calibration, require stable cold junction temperature.
RTDs:
- Pros: Highly accurate, good stability, no need for a reference junction.
- Cons: Limited temperature range (not ideal for extreme temperatures), slower response time, typically more expensive than thermocouples.
So, which one to choose?
- For high-precision applications where accuracy is crucial (like in a lab setting), an RTD might be better.
- For a wider temperature range or if you need a fast response time (think monitoring a furnace), a thermocouple is a good option.
- For cost-effectiveness, thermocouples are generally the more budget-friendly choice.
What is the IEC standard for thermocouples?
The primary standard for thermocouple color coding within the UK and Europe is BS EN 60584, specifically part 3:2008 (BS EN 60584-3:2008).
It’s important to note that while this standard is often referred to as the “IEC color code,” the technical term is BS EN 60584. This standard defines the specific colour codes assigned to different thermocouple types for easy identification.